This HD video introduces the five practice exercises that you will find on the click links (below).
1) Simple gas beads and tack welds
2) Improving your gas welding beads
3) Gas welds in vertical and overhead position
As these final exercises demonstrate, gas welding can provide the strength, fusion quality and base metal compatibility found with other welding processes. Gas welding still serves some types of pressure vessel work, high pressure pipe repairs and other niche tasks.
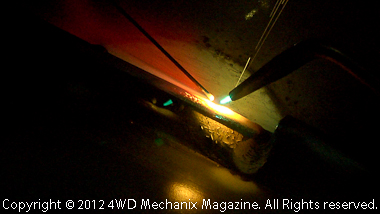
Gas welding has been around for over a century now. The process lends itself to niche uses, like auto body work, tubing and fitting tasks, industrial tool repairs and small parts restoration. Unlike brazing, oxy-acetylene welding is a bona fide metal fusion process.
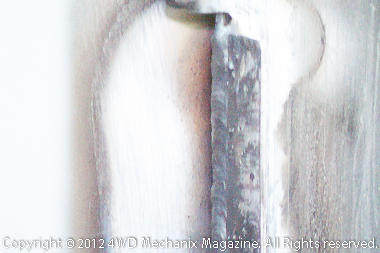
As the filler tube holder project illustrates, gas welds can resemble MIG or TIG welds. Above is a bead run with oxy-acetylene process and ER70-S2 filler rod. Strong and reliable, this weld matches the integrity of any other fusion welding process.
There are lessons in gas welding that apply to all other forms of fusion welding. Although the rush is to MIG or TIG machines, those who take the time to study and practice oxy-acetylene gas welding will be well rewarded. Gas welding is the first type of welding taught in traditional welding schools and classes. Oxy-acetylene welding is a valued foundation skill.
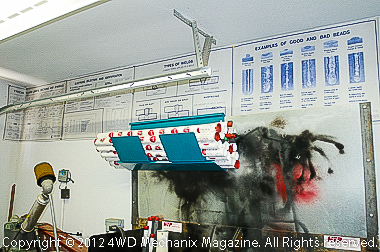
The filler tube rack (above) is a product of gas welding. This project took less than an hour to complete, converting a catalog rack into a functional holder for Weld Mold Company’s filler rod canisters. As seen in the illustrations below, gas welding process can produce very strong welds, with results similar to other fusion welding methods.
For those following the ‘How-to: Welding Class’ coverage of gas welding and brazing processes, the sub-pages in this section contain useful practice exercises for gas welding. Take the time to view these HD videos, they offer insights that apply to every kind of fusion welding.

The catalog stand had wings at each end. Turned into craddle flanges, the “wings” are positioned for tack welding. Paint removed from the weld joint, tack welding can now begin.
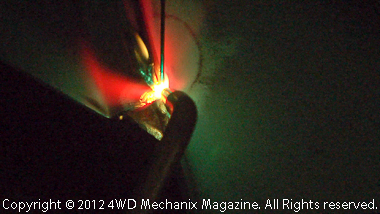
The two wings get tack welded into position as with any other welding process. With this gauge metal, we use ER70-S2 in 3/32″ diameter. In the HD videos covering gas welding exercises
you can watch the welding process in real time!
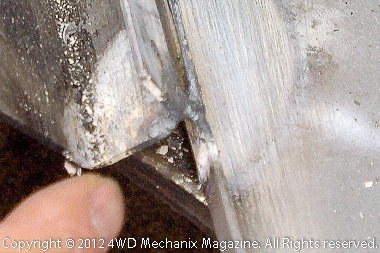
Strong tack welds at each end of the wing will support the wing as we run the welding bead. This is similar to stick, MIG or TIG tack welds. ER70-S2 filler rod material has 83K PSI tensile and 70K shear or yield strength.
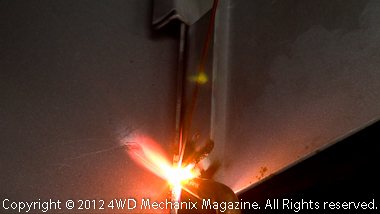
Here, welding filler material dips into the molten weld puddle, similar to TIG process. Gas torch with a #2 tip heats the metal evenly to the liquid point. Filler melts upon hitting the liquid puddle.
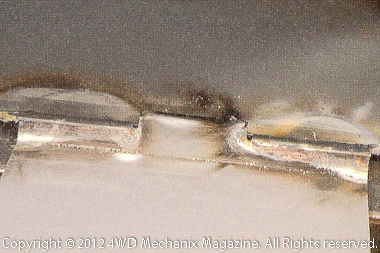
Finish beads are both strong and equal in stamina to MIG, stick or TIG. Gas welding is slower but very functional for smaller parts and even field service work. The only downside is the diffused heat pouring into the metal, which tends to create a wider heat affected zone (HAZ).
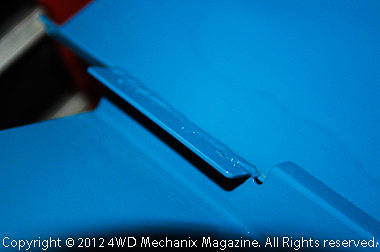
Yes, this is actually a gas welded bead! The formation looks much like MIG, with full fusion of the metal parts and buildup of filler metal in a uniform crown. The canister holder is now painted and ready for service.

What appears to be a “weld bead” here is actually the backside of the weld! Yes, the pentration is that good in this case. The weld has a normal crown (on opposite side) that provides exceptional strength and a deep weld joint. Back side “weld” is in part due to the intentional, slight gap placed between the two pieces prior to welding.